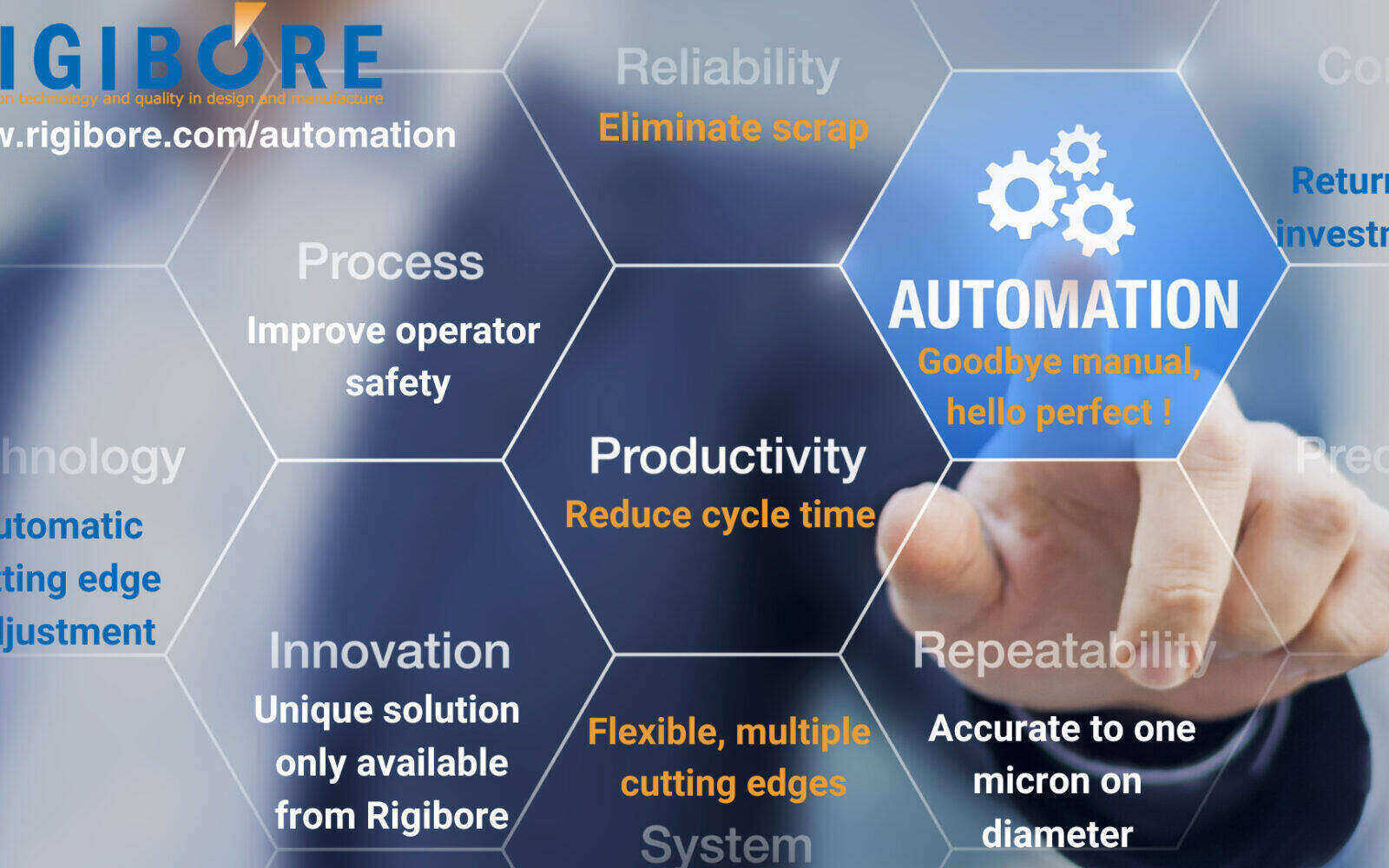
How to automatically adjust boring bars to 1 micron accuracy: A Game-Changer in Precision Machining
Date Posted: 4th April
Categories: Automation and General News.
In precision machining, hitting micron-level accuracy is vital. Making engine parts, aerospace components, or medical devices?
Setting the cutting edge precisely can revolutionize your production process. Let’s explore how advanced tech enables automatic adjustments, enhances efficiency, reduces waste, and ensures operator safety.
USING THE MACHINE CONTROL TO MAKE CUTTING EDGE ADJUSTMENTS
Traditionally, adjusting a boring bar involves manual intervention. Operators meticulously measured and tweaked the tool’s position to achieve the desired diameter. However, this process is time-consuming, error-prone and often leads to variations in bore size. Enter ActiveEdge, a groundbreaking solution that uses the machine control to make in-process adjustments.
ActiveEdge Features:
Adjustable Cartridges: Each cartridge moves independently, following precise commands.
Faster Cutting: Operators can adjust the insert quickly without taking the bar off the machine.
Maximized Insert Life: Accurate adjustments ensure longer insert lifespan, minimizing downtime.
SCRAP REDUCTION FROM CONSISTENT ACCURACY
Scrap is the bane of any manufacturing process. Inaccurate bore sizes lead to rejected parts, wasted materials, and increased costs. With ActiveEdge, you can ensure precise results, reducing scrap waste. Machining crankshaft bearing journals or aerospace components, hitting target diameter is crucial. It ensures quality and saves cost.
BOOSTED PRODUCTIVITY: NO MORE MANUAL TOOL ADJUSTMENTS
Imagine a production line where boring bars automatically adapt to changing conditions. ActiveEdge makes this a reality. By eliminating manual adjustments, you free up valuable operator time. Whether it’s a high-volume run or a complex prototype, the system adapts seamlessly, allowing your team to focus on other critical tasks.
OPERATOR SAFETY – STAYING OUTSIDE THE MACHINE ENVELOPE
Safety is non-negotiable in any manufacturing environment. ActiveEdge improves operator safety by eliminating the need to enter the machine during adjustments. No more reaching into tight spaces or risking injury. The system’s wireless capabilities allow adjustments from a safe distance, ensuring a secure working environment.
CONCLUSION
Precision machining demands innovation. ActiveEdge’s micron-accurate adjustments redefine what’s possible. Whether you’re a seasoned machinist or a production manager, embracing this technology ensures consistent quality, safety, and a competitive edge in today’s manufacturing landscape.
Immediate ROI: Faster cycle time, less scrap
Investing in ActiveEdge pays off swiftly. Here’s how:
Decreased Cycle Time: Faster adjustments mean shorter machining cycles, translating to increased throughput.
Reduced Scrap Rates: Accurate adjustments lead to fewer rejected parts, saving material costs.
Enhanced Efficiency: Operators can focus on value-added tasks, driving overall productivity.
Discover more about ActiveEdge and its technical specifications here
Remember, when it comes to precision boring, microns matter—and ActiveEdge delivers.
Related
Posts...